Moderne Schweizer Staubentsorgung
Die in Luzern ansässige NBS AG erhält den Grossauftrag der Kunert Wellpappe in Biebesheim und realisiert die komplette Lüftungs- und Staubentsorgung zur neuen Göpfert Wellpappen-Verarbeitungsmaschine.
Was haben die Firma NBS AG, ein Schweizer Unternehmen mit Spezialisierung auf Absaug- und Entsorgungstechnik, und die Kunert Gruppe, ein international führender Hersteller von Hülsen und Verpackungen aus Wellpappe, gemeinsam?
Nun, beide sind familiengeführte Traditionsfirmen und beide sind innovativ mit ihren Produkten und Dienstleistungen unterwegs. Das grösste gemeinsame Merkmal ist jedoch, dass beide Unternehmen jeweils das konstruktivste Lösungskonzept verfolgen. So hat sich die Kunert Gruppe im November 2019 für das Staubentsorgungsprojekt der Firma NBS AG, Nickel Betriebsanlagen + Systeme, entschieden.
Ein professionelles Anlagenkonzept
Zur Kunert Gruppe gehören 17 Werke mit insgesamt rund 2.000 Mitarbeitern, davon sind 2 Werke auf die Produktion von Wellpappe spezialisiert. Diese werden in ein- bis dreiwelligen Qualitäten hergestellt, bedruckt und zu individuellen Verpackungen verarbeitet. Um die wachsende Nachfrage von Wellpappe-Produkten abdecken zu können, hat sich die Kunert Gruppe entschieden, in eine neue Wellpappen-Verarbeitungsmaschine CL 13/32 von Bahmüller-Göpfert (BGM) zu investieren. Bereits im Sommer 2019 begann die Evaluationsphase für die neue Absauganlage. Die Aufgabenstellung: Rund 50.000 m3/h kontaminierte Luft muss von der Maschine weggebracht und entsprechend verarbeitet werden. Zusätzlich müssen auch die Stanzabfälle zum bestehenden Entsorgungsplatz befördert werden. Zu diesem Zeitpunkt war der Plan, eine baugleiche Absaugung mit Monoblock-Feinfiltrierung, wie sie bereits auf dem Nebenplatz steht, aufzustellen. „Nach den Gesprächen mit Herr Jörg Nickel waren wir aber sehr schnell an den Alternativen interessiert“, so Andreas Goldbach, technischer Leiter der Wellpappengruppe.
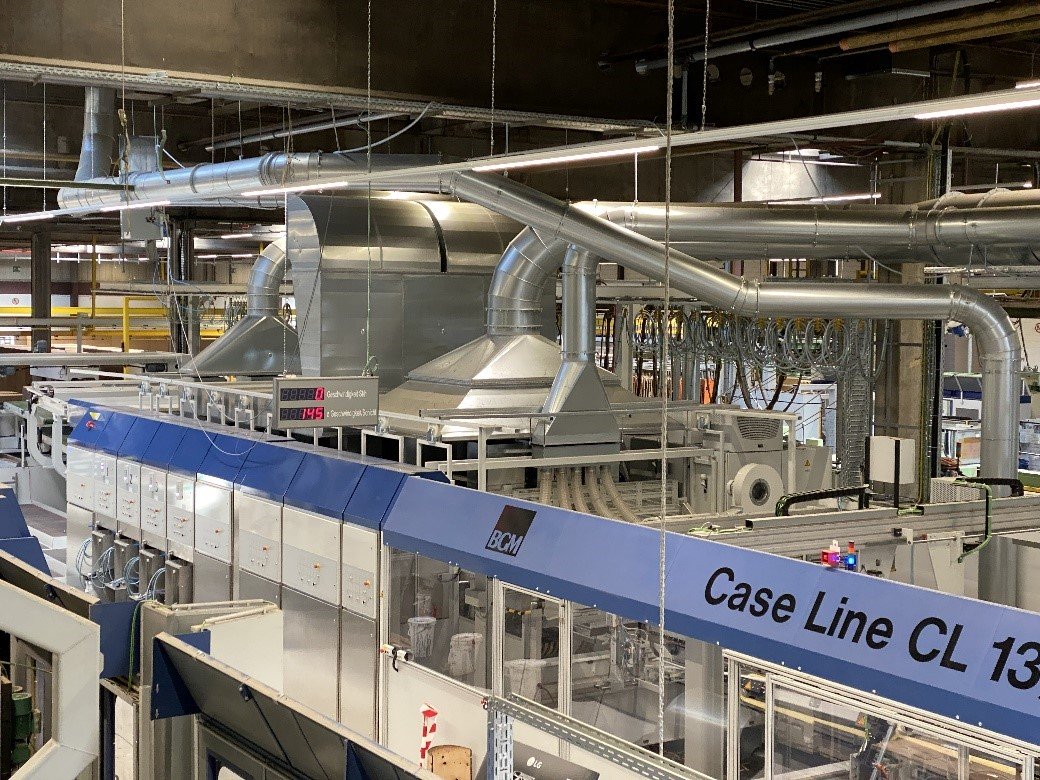
Mittels modernster Ventilatoren- und Steuerungstechnik wird nun ab April 2020 die staubhaltige Luft der Verarbeitungsmaschine in eine speziell konstruierte NBS Jet-Set-Filteranlage befördert. Dort fangen mehr als 300 Filtersäcke die kontaminierte Luft auf, die dann mittels Druckluft abgeschossen werden. Der anfallende Staub wird in einem Silo aufgefangen und in einer Brikettierpresse zu harten Briketts verpresst. Die gereinigte Luft gelangt schlussendlich in die Produktionshalle zurück. Jörg Nickel, Geschäftsführer der Firma NBS AG, erklärt sein Konzept: „Wir probieren jeweils immer, für unsere Kunden ein nachhaltiges und zu Ende gedachtes Konzept zu kreieren. Denn schliesslich sind wir die Spezialisten und kennen die langfristigen Vor- und Nachteile von verschiedenen Absaugsystemen. Mit dem hier gewählten Ansatz hat die Kunert Gruppe eine professionelle Absauganlage, mit welcher sie nahezu nichts mehr zu tun hat. Alles wird automatisch geregelt und die Filtersäcke müssen nicht mehr so oft gewechselt werden wie die Feinfilterzellen.“
Aufbau während Krisenzeit innerhalb 6 Wochen
Die Corona Krise überraschte die Wirtschaft in allen Bereichen. So wurde mit dem Lockdown und den Grenzschliessungen auch die Montageinstallation für die NBS eine grosse Herausforderung. Doch die gesamte Montage konnte, unter Berücksichtigung der Hygiene- und Abstandsmaßnahmen, vom NBS-Deutschland-Montageteam termingerecht durchgeführt werden. Jürgen Prell, Geschäftsführer Kunert Biebesheim, hält fest: „Der Termin für die Abnahme der Verarbeitungsmaschine stand seit Anfang des Jahres fest, da gab es nichts mehr zu rütteln. Zum Glück war die Firma NBS so gut aufgestellt und konnte die Absauganlage trotz der nicht vorhersehbaren Beschränkungen durch die Pandemie pünktlich wie vereinbart in Betrieb nehmen. Wir sind sehr zufrieden und freuen uns über die hervorragende partnerschaftliche Zusammenarbeit mit der NBS“.
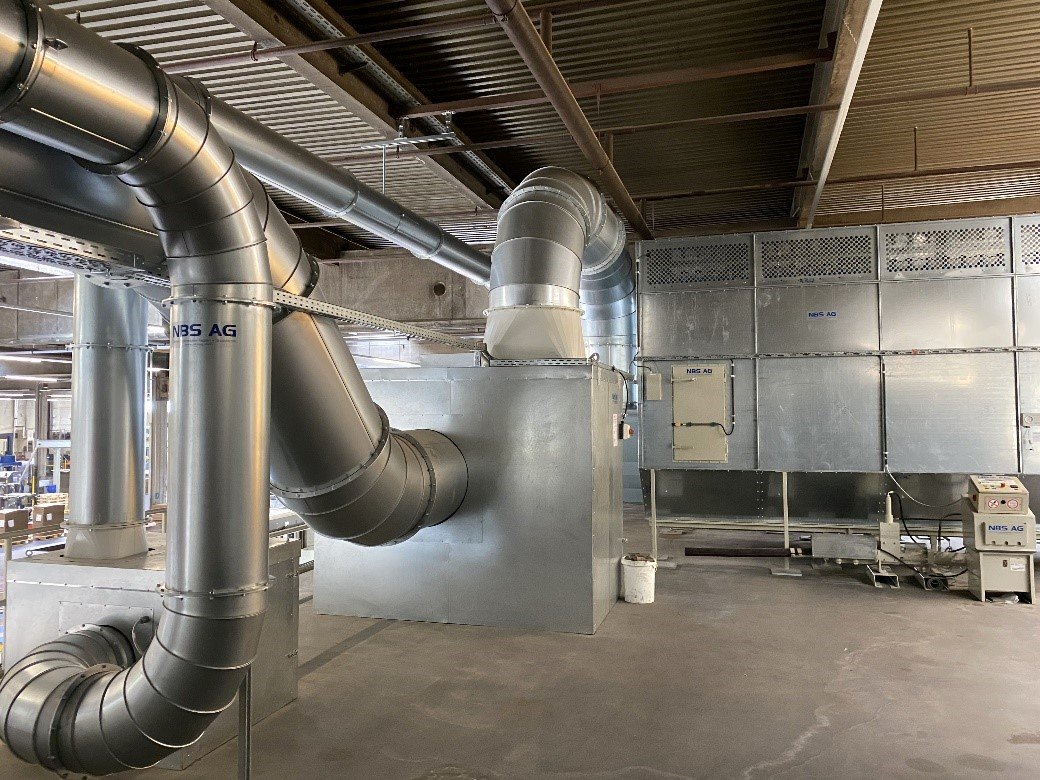